A while back I made a jumper using some nice black cotton with a waffle weave finish. I used a pattern that was apparently in my size but when it was finished, the jumper looked more like a tent and as the hem grazed my ankles, I thought, not even taking it up will help. I really needed to be about 6 feet tall to make that pattern work. So I am going to give it away to the Sally Ann when I can bear to part with it - never-been-worn and nicely made. Ah well.
When I got the fabric, I bought yards of it because - that's right! - it was on sale. I decided that I could now use a serviceable black skirt so I hauled out what was left and cut out the skirt in the pattern I love - New Look 6462.

Having cut out the skirt, I realized there was still a lot of the fabric left over and it struck me that I could make a little jacket that would work like a cardigan.

I trotted out the "shrunken jacket" pattern Simplicity 4698 and decided to see if View C in the 3/4 sleeve would fit on what was left. I've made this pattern before and if I'm not too fat, it looks pretty cute on me. Because it is unlined, I thought it would feel more like a cardigan.

Veiw C and D don't have lapels and I didn't have enough fabric for them, so I decided a little piping would liven the jacket up.
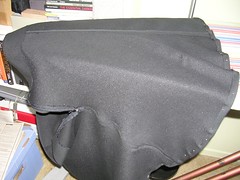
Here's the skirt, ready for hemming. The fabric has a dull side and a slightly shiny side and I put the dull side as the right side. In spite of it being cotton, it also doesn't make a narrow fold very well and so I had to use pins to hold the hem down before sewing it.

Here it is, finished and hanging up. I have a boom box parked in front of my sewing room door and am too lazy to move it so the photo looks odd. I have been listening to CBC French radio in the hopes that the language will impart itself to me by osmosis and am using the boom box instead of my usual radio because the old dial on the usual radio is very fiddly and I don't like to change it from the English CBC, otherwise all I get is static.
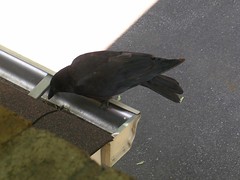
Finally, when I was in my sewing room yesterday, I heard the sound of toenails on metal and looked out the window to see a local crow picking at something in the rain gutters. Although they are noisy (especially at 6 am) and they pick holes in my garbage bags, I like the bold birds and so I took his picture instead of shooing him away.