
The bags were a hit! I gave away all six large totes and some of the smaller zipped bags and people seemed happy to have them. Back tracking a few days -- I also made the two little rectangular bags above, just for fun. I thought because they were dark, some of the men might like one. Some of the men did take a couple of the small bags as I hoped, for small tools and things. One even mentioned allen wrenches, which is what Peter keeps in his.
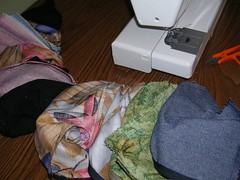
All the little zipped bags are built the same so I just sew one part on all of them at once, like an assembly line. Here, I am sewing a corner at the bottom and I don't bother to cut the threads between the bags until I am finished all of them.

I cut the bags out with pinking shears so the raw edges wouldn't fray too much. On the small bags, because I cut them out a couple of years ago, I hadn't used pinking shears so I trimmed all the edges after I sewed them. My sewing room is now buried under layers of tiny pills or puffs from the pinking. I am going to have to do a thorough vacuuming before I start my next project.

Here are the other three large totes that I made, after I changed the thread from white to black in my machine.

And here are all the bags at once, ready to be taken down to the family reunion. I had a fun time making them and a fun time giving them away. I also gave the "suede" jacket to my niece and she seemed to like it very much. She even wore it later, when it got a little cool. But I totally forgot to take a picture of her wearing it! I can't believe I did that. Next time.